Fluids Review Design¶
This section is meant to be a refresher on fluid mechanics. It will only cover the topics of fluids mechanics that will be used heavily in the course.
If you wish to review fluid mechanics in (much) more detail, please refer to this guide. If you wish to review from a legitimate textbook, you can find a pdf of good book by Frank White here.
Important Terms and Equations¶
Terms:
- Head
- Streamline
- Head loss
- Laminar
- Turbulent
- Moody Diagram
- Viscosity
- Driving head
- Vena Contracta/Coefficient of Contraction
Equations:
- Bernoulli equation
- Energy equation
- Darcy-Weisbach equation
- Reynolds number
- Swamee-Jain equation
- Hagen-Poiseuille equation
- Orifice equation
Introductory Concepts¶
Before diving in to the rest of the fluids review document, there are a few important concepts which will be the foundation for building your understanding of fluid mechanics. One must walk before they can run, and similarly, the basics of fluid mechanics must be understood before moving on to the more fun sections of this document.
Continuity Equation¶
Continuity is simply an application of mass balance to fluid mechanics. It states that the cross sectional area A that a fluid flows through multiplied by the fluid’s average flow velocity ˉv must equal the fluid’s flow rate Q:
Note
The line above the v is called a ‘bar,’ and represents an average. Any variable can have a bar. In this case, we are adding the bar to velocity v, turning it into average velocity ˉv. This variable is pronounced ‘v bar.’
In CEE 4540, we deal primarily with flow through pipes. For a circular pipe, A=πr2. Substituting diameter in for radius, r=D2, we get A=πD24. You will often see this form of the continuity equation being used to relate the flow rate in a pipe to the fluid velocity and pipe diameter:
The continuity equation is also useful when flow is going from one geometry to another. In this case, the flow in one geometry must be the same as the flow in the other, Q1=Q2, which yields the following equations:
An example of changing flow geometries is when the a change in pipe size occurs in a circular piping system, as is demonstrated below. The flow through pipe1 must be the same as the flow through pipe2.
Laminar and Turbulent Flow¶
Considering that this class deals with the flow of water through a water treatment plant, understanding the characteristics of the flow is very important. Thus, it is necessary to understand the most common characteristic of fluid flow: whether it is laminar or turbulent. Laminar flow is very smooth and highly ordered. Turbulent flow is chaotic, messy, and disordered. The best way to understand each flow and what it looks like is visually, like in this video or the wikipedia image below. Please ignore the part of the video after the image of the tap.
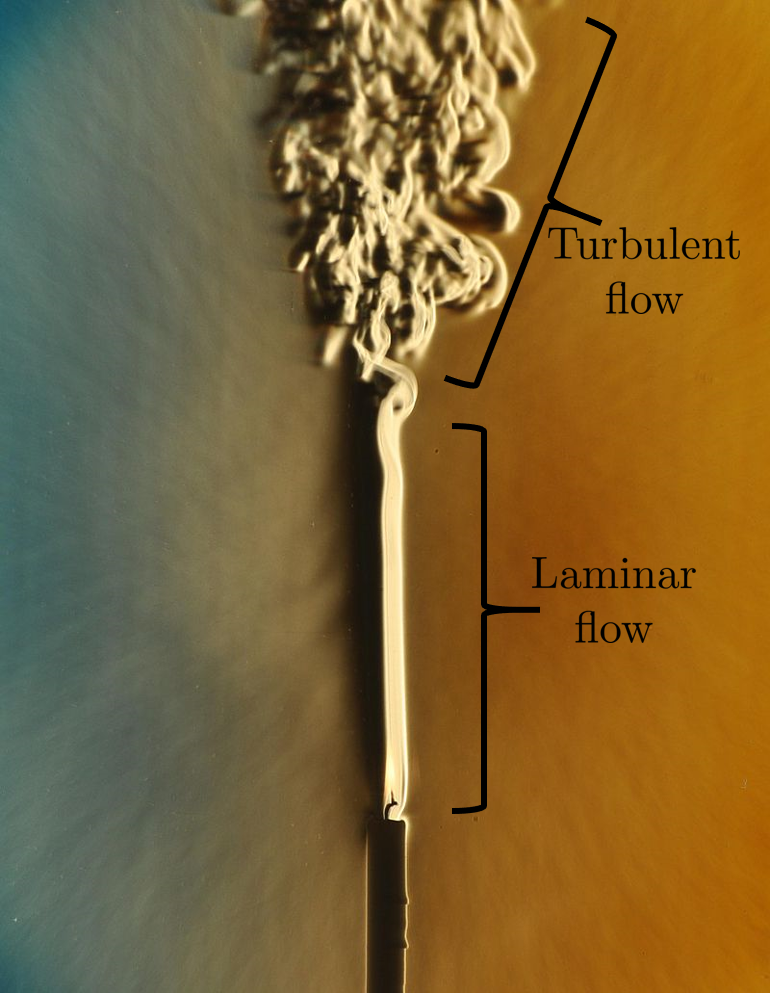
Fig. 4 This is a beautiful example of the difference between ordered, smooth laminar and chaotic turbulent flow.
A numeric way to determine whether flow is laminar or turbulent is by finding the Reynolds number, Re. The Reynolds number is a dimensionless parameter that compares inertia, represented by the average flow velocity ˉv times a length scale D to viscosity, represented by the kinematic viscosity ν. Click here for a brief video explanation of viscosity. If the Reynolds number is less than 2,100 the flow is considered laminar. If it is more than a certain value, it is considered turbulent.
There is a transition between laminar and turbulent flow which is not yet well understood. To simplify this phenomenon and make it possible to code for laminar or turbulent flow, we assume that the transition occurs at Re=2100. The flow regime is assumed to be laminar below this value and turbulent above it. This variable is coded into aide_design as pc.RE_TRANSITION_PIPE
. We will neglect transitional flow.
Fluid can flow through very many different geometries like a pipe, a rectangular channel, or any other shape. To account for this, the characteristic length scale is quantified as the hydraulic diameter, which can be applied to any geometry. For circular pipes, which are the most common geometry you’ll encounter in this class, the hydraulic diameter is simply the pipe diameter.
Here are other commonly used forms of the Reynolds number equation. They are the same as the one above, just with the substitutions Q=ˉvπD24 and ν=μρ
See also
Function in aide_design: pc.re_pipe(FlowRate, Diam, Nu)
Returns the Reynolds number in a circular pipe. Functions for finding the Reynolds number through other conduits and geometries can also be found in physchem.py within aide_design.
Note
Laminar and turbulent flow are described as two different flow regimes. When there is a characteristic of flow and different categories of the characteristic, each category is referred to as a flow regime. For example, the Reynolds number describes a flow characteristic, and its categories, referred to as flow regimes, are laminar or turbulent.
Streamlines and Control Volumes¶
Both streamlines and control volumes are tools to compare different sections of a system. For this class, this system will always be hydraulic.
Imagine water flowing through a pipe. A streamline is the path that a particle would take if it could be placed in the fluid without changing the original flow of the fluid. A more technical definition is “a line which is everywhere parallel to the local velocity vector.” Computational tools, dyes (in water), or smoke (in air) can be used to visualize streamlines.
A control volume is just an imaginary 3-dimensional shape in space. Its boundaries can be placed anywhere by the person applying the control volume, and once set the boundaries remain fixed in space over time. These boundaries are usually chosen to compare two relevant surfaces to each other. The entirety of a control volume is usually not shown, as it is often unnecessary. This is shown in the following image:
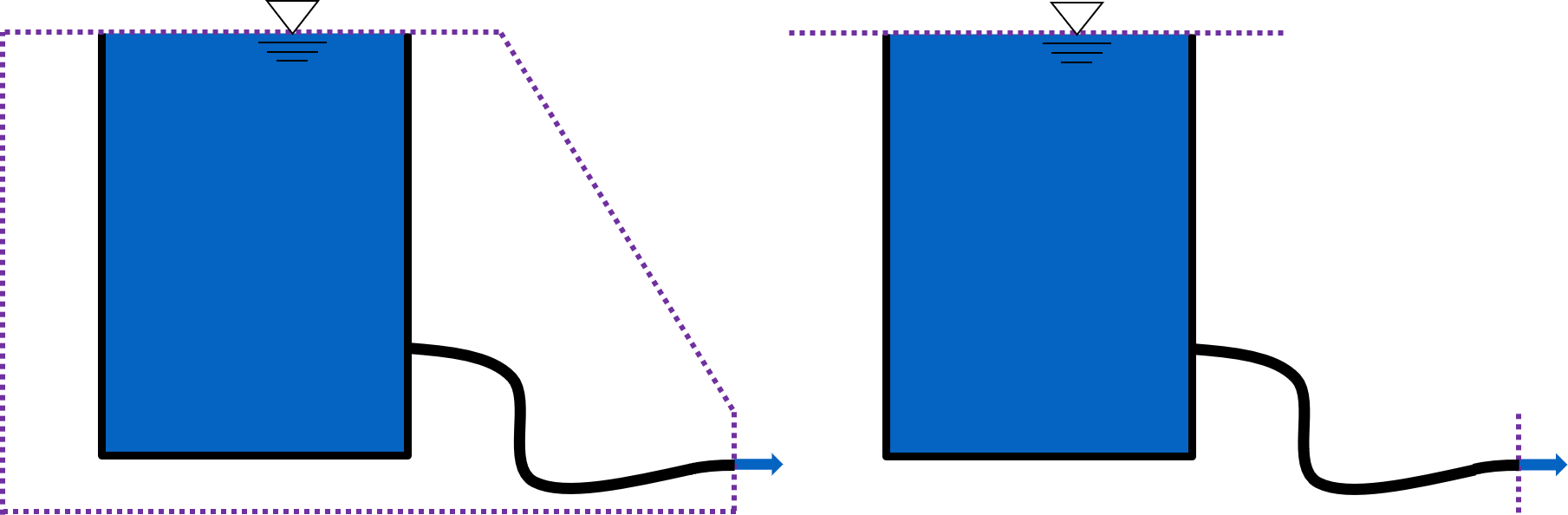
Fig. 5 While the image on the left indicates a complete control volume, control volumes are usually shortened to only include the relevant surfaces, in which the control volume intersects the fluid. This is shown in the image on the right.
Important
Many images will be used over the course of this class to show hydraulic systems. A standardized system of lines will be used throughout them all to distinguish reference elevations from control volumes from streamlines. This system is described in the image below.
The Bernoulli and Energy Equations¶
As explained in CEE 3310 with more details than most of you wanted to know, the Bernoulli and energy equations are incredibly useful in understanding the transfer of the fluid’s energy throughout a streamline or through a control volume. The Bernoulli equation applies to two different points along one streamline, whereas the energy equation applies across a control volume. The energy of a fluid has three forms: pressure, potential (deriving from elevation), and kinetic (deriving from velocity).
The Bernoulli Equation¶
These three forms of energy expressed above make up the Bernoulli equation:
pc.gravity
Notice that each term in this form of the Bernoulli equation has units of [L], even though the terms represent the energy of water, which has units of [M]⋅[L]2[T]2. When energy of water is described in units of length, the term used is called head.
There are two important distinctions to keep in mind when using head to talk about energy. First is that head is dependent on the density of the fluid under consideration. Take mercury, for example, which is around 13.6 times more dense than water. 1 meter of mercury head is therefore equivalent to around 13.6 meters of water head. Second is that head is independent of the amount of fluid being considered, as long as all the fluid is the same density. Thus, raising 1 liter of water up by one meter and raising 100 liters of water up by one meter are both equivalent to giving the water 1 meter of water head, even though it requires 100 times more energy to raise the hundred liters than to raise the single liter. Since we are concerned mainly with water in this class, we will refer to ‘water head’ simply as ‘head’.
Going back to the Bernoulli equation, the pρg term is called the pressure head, z the elevation head, and v22g the velocity head. The following diagram shows these various forms of head via a 1 meter deep bucket (left) and a jet of water shooting out of the ground (right).
Assumption in using the Bernoulli equation¶
Though there are many assumptions needed to confirm that the Bernoulli equation can be used, the main one for the purpose of this class is that energy is not gained or lost throughout the streamline being considered. If we consider more precise fluid mechanics terminology, then “friction by viscous forces must be negligible.” What this means is that the fluid along the streamline being considered is not losing energy to viscosity. Energy can only be transferred between its three forms if this equation is to be used, it can’t be gained or lost.
Example problems¶
Here is a simple worksheet with very straightforward example problems using the Bernoulli equation. Note that the solutions use the pressure-form of the Bernoulli equation. This just means that every term in the equation is multiplied by ρg, so the pressure term is just P. The form of the equation does not affect the solution to the problem it helps solved.
The Energy Equation¶
The assumption necessary to use the Bernoulli equation, which is stated above, represents the key difference between the Bernoulli equation and the energy equation for the purpose of this class. The energy equation accounts for the (L)oss of energy from both the fluid flowing, hL, and any other energy drain, like the charging of a (T)urbine, hT. It also accounts for any energy inputs into the system, hP, which is usually caused by a (P)ump within the control volume.
You’ll also notice the α term attached to the velocity head. This is a correction factor for kinetic energy, and will be neglected in this class. In the Bernoulli equation, the velocity of the streamline of water is considered, v. The energy equation, however compares control surfaces instead of streamlines, and the velocities across a control surface many not all be the same. Hence, ˉv is used to represent the average velocity. Since AguaClara does not use pumps nor turbines, hP=hT=0. With these simplifications, the energy equation can be written as follows:
This is the form of the energy equation that you will see over and over again in CEE 4540. To summarize, the main difference between the Bernoulli equation and the energy equation for the purposes of this class is energy loss. The energy equation accounts for the fluid’s loss of energy over time while the Bernoulli equation does not. So how can the fluid lose energy?
Headloss¶
Head(L)oss, hL is a term that is ubiquitous in both this class and fluid mechanics in general. Its definition is exactly as it sounds: it refers to the loss of energy of a fluid as it flows through space. There are two components to head loss: major losses caused by pipe-fluid (f)riction, hf, and minor losses caused by fluid-fluid friction resulting from flow (e)xpansions, he, such that hL=hf+he.
Major Losses¶
These losses are the result of friction between the fluid and the surface over which the fluid is flowing. A force acting parallel to a surface is referred to as shear. It can therefore be said that major losses are the result of shear between the fluid and the surface it’s flowing over. To help in understanding major losses, consider the following example: imagine, as you have so often in physics class, pushing a large box across the ground. Friction is what resists your efforts to push the box. The farther you push the box, the more energy you expend pushing against friction. The same is true for water moving through a pipe, where water is analogous to the box you want to move, the pipe is similar to the floor that provides the friction, and the major losses of the water through the pipe is analogous to the energy you expend by pushing the box.
In this class, we will be dealing primarily with major losses in circular pipes, as opposed to channels or pipes with other geometries. Fortunately for us, Henry Darcy and Julius Weisbach came up with a handy equation to determine the major losses in a circular pipe under both laminar and turbulent flow conditions. Their equation is logically but unoriginally named the Darcy-Weisbach equation and is shown below:
Substituting the continuity equation Q=ˉvA in the form of ˉv2=16Q2π2D4 gives another, equivalent form of Darcy-Weisbach which uses flow, Q, instead of velocity, ˉv:
See also
Function in aide_design: pc.headloss_fric(FlowRate, Diam, Length, Nu, PipeRough)
Returns only major losses. Works for both laminar and turbulent flow.
Darcy-Weisbach is wonderful because it applies to both laminar and turbulent flow regimes and contains relatively easy to measure variables. The one exception is the Darcy friction factor, f. This parameter is an approximation for the magnitude of friction between the pipe walls and the fluid, and its value changes depending on the whether or not the flow is laminar or turbulent, and varies with the Reynolds number in both flow regimes.
For laminar flow, the friction factor can be determined from the following equation:
For turbulent flow, the friction factor is more difficult to determine. In this class, we will use the Swamee-Jain equation:
See also
Function in aide_design: pc.fric(FlowRate, Diam, Nu, PipeRough)
Returns f for laminar or turbulent flow. For laminar flow, use ‘0’ for the PipeRough
input.
The simplicity of the equation for f during laminar flow allows for substitutions to create a very useful, simplified equation for major losses during laminar flow. This simplification combines the Darcy-Weisbach equation, the equation for the Darcy friction factor during laminar flow, and the Reynold’s number formula:
To form the Hagen-Poiseuille equation for major losses during laminar flow, and only during laminar flow:
The significance of this equation lies in its relationship between hf and Q. Hagen-Poiseuille shows that the terms are directly proportional (hf∝Q) during laminar flow, while Darcy-Weisbach shows that hf grows with the square of Q during turbulent flow (hf∝Q2). As you will soon see, minor losses, he, will grow with the square of Q in both laminar and turbulent flow. This has implications that will be discussed later, in the flow control section.
In 1944, Lewis Ferry Moody plotted a ridiculous amount of experimental data, gathered by many people, on the Darcy-Weisbach friction factor to create what we now call the Moody diagram. This diagram has the friction factor f on the left-hand y-axis, relative pipe roughness ϵD on the right-hand y-axis, and Reynolds number Re on the x-axis. The Moody diagram is an alternative to computational methods for finding f.
Minor Losses¶
Unfortunately, there is no simple ‘pushing a box across the ground’ example to explain minor losses. So instead, consider a hydraulic jump. In the video, you can see lots of turbulence and eddies in the transition region between the fast, shallow flow and the slow, deep flow. The high amount of mixing of the water in the transition region of the hydraulic jump results in significant friction between water and water (recall that the measure of a fluid’s resistance to internal, fluid-fluid friction is called viscosity). This turbulent, eddy-induced, fluid-fluid friction results in minor losses, much like fluid-pipe friction results in major losses.
As is the case in a hydraulic jump, a flow expansion (from shallow flow to deep flow) creates the turbulent eddies that result in minor losses. This will be a recurring theme in throughout the course: minor losses are caused by flow expansions. Imagine a pipe fitting that connects a small diameter pipe to a large diameter one, as shown in the image below. The flow must expand to fill up the entire large diameter pipe. This expansion creates turbulent eddies near the union between the small and large pipes, and these eddies cause minor losses. You may already know the equation for minor losses, but understanding where it comes from is very important for effective AguaClara plant design. For this reason, you are strongly recommended to read through the full derivation, in Fluids Review Derivations.
There are three forms of the minor loss equation that you will see in this class:
pc.headloss_exp_general(Vel, KMinor)
Returns he. Can be
either the second or third form due to user input of both velocity and
minor loss coefficient. It is up to the user to use consistent
ˉv and Ke.pc.headloss_exp(FlowRate, Diam, KMinor)
Returns he. Uses
third form, Ke.Note: You will often see K′e and Ke used without the e subscript, they will appear as K′ and K.
The in and out subscripts in each of the three forms refer to the diagram that was used for the derivation:
The second and third forms are the ones which you are probably most familiar with. The distinction between them, however, is critical. First, consider the magnitudes of Ain and Aout. Ain can never be larger than Aout, because the flow is expanding. When flow expands, the cross-sectional area it flows through must increase. As a result, both AoutAin>1 and AinAout<1 must always be true. This means that K′ can never be greater than 1, while K technically has no upper limit.
If you have taken CEE 3310, you have seen tables of minor loss coefficients like this one, and they almost all have coefficients greater than 1. This implies that these tables use the third form of the minor loss equation as we have defined it, where the velocity is ˉvout. There is a good reason for using the third form over the second one: ˉvout is far easier to determine than ˉvin. Consider flow through a pipe elbow, as shown in the image below.
In order to find ˉvout, we first need to know which point is out and which point is in. A simple way to distinguish the two points is that in occurs when the flow is most contracted, and out occurs when the flow has fully expanded after that maximal contraction. Going on these guidelines, point ‘B’ above would be in, since it represents the most contracted flow in the elbow-pipe system. Therefore point ‘C’ would be out, as it is the point where the flow has fully expanded after its compression in ‘B.’
ˉvout is easy to determine because it is the velocity of the fluid as it flows through the entire area of the pipe. Thus, ˉvout can be found with the continuity equation, since the flow through the pipe and its diameter are easy to measure, ˉvout=4QπD2. On the other hand, ˉvin is difficult to find, as the area of the contracted flow is dependent on the exact geometry of the elbow. This is why the third form of the minor loss equation, as we have defined it, is the most common.
Head Loss = Elevation Difference Trick¶
This trick, also called the ‘control volume trick,’ or more colloquially, the ‘head loss trick,’ is incredibly useful for simplifying hydraulic systems and is used all the time in this class.
Consider the following image, which was taken from the Flow Control and Measurement powerpoint.
In systems like this, where an elevation difference is causing the flow of water, the elevation difference is called the driving head. In the system above, the driving head is the elevation difference between the water level and the end of the tubing. Usually driving head is written as Δz or Δh, though above it is labelled as hL.
This image is violating the energy equation by saying that the elevation difference between the water in the tank and the end of the tube is hL. It implies that all of the driving head, Δz, is lost to head loss and therefore that no water is flowing out of the tubing, which is not true. Let’s apply the energy equation between the two red points. Pressures are atmospheric at both points and the velocity of water at the top of tank is negligible.
We now get:
This contradicts the image above, which says that Δz=hL and neglects ˉv222g. The image above is correct, however, if you apply the head loss trick. The trick incorporates the ˉv222g term into the hL term as a minor loss. See the math below:
This last step incorporated the kinetic energy term of the energy equation, ˉv222g, into the minor loss equation by saying that its K is 1. From here, we reverse our steps to get Δz=hL
By applying the head loss trick, you are considering the entire flow of water out of a control volume as lost energy. This is just an algebraic trick, the only thing to remember when applying this trick is that ∑K will always be at least 1, even if there are no ‘real’ minor losses in the system.
The Orifice Equation¶
This equation is one that you’ll see again and again throughout this class. Understanding it now will be invaluable, as future concepts will use and build on this equation.
Vena Contracta¶
Before describing the equation, we must first understand the concept of a vena contracta. Refer once more to this image of flow through a pipe elbow.
The flow contracts as the fluid moves from point ‘A’ to point ‘B.’ This happens because the fluid can’t make a sharp turn at the corner of the elbow. Instead, the streamline closest to the sharp turn makes a slow, gradual change in direction, as shown in the image. As a result of this gradual turn, the cross-sectional area the fluid is flowing through at point ‘B’ is less than the cross-sectional area it flows through at points ‘A’ and ‘C’. Written as an equation, AcsB<AcsA=AcsC, where the csA stands for ‘control surface A’ subscript
The term ‘vena contracta’ describes the phenomenon of contracting flow due to streamlines being unable to make sharp turns. Πvc is a ratio between the flow area at the vena contracta, AcsB, which is when the flow is maximally contracted, and the flow area before the contraction, AcsA. In the image above, the equation for the vena contracta coefficient would be:
Note that what this class calls Πvc is often referred to as
a ‘Coefficient of Contraction,’ Cc, in other engineering
courses and settings. When the most extreme turn a streamline must make
is 90°, the value of the vena contracta coefficient is close to 0.62.
This parameter is in aide_design as pc.RATIO_VC_ORIFICE
. The vena
contracta coefficient value is a function of the flow geometry.
A vena contracta coefficient is not a minor loss coefficient. Though the equations for the two both involve contracted and non-contracted areas, these coefficients are not the same. Refer to the flow through a pipe elbow image above. The minor loss coefficient equation uses the areas of points ‘B’ and ‘C,’ while the vena contracta coefficient uses the areas of points ‘A’ and ‘B.’ Additionally, the equations to calculate the coefficients themselves are not the same. Confusing the two coefficients is common mistake that this paragraph will hopefully help you to avoid.
Origin¶
The orifice equation is derived from the Bernoulli equation as applied to the red points in the following image:
At point A, the pressure is atmospheric and the instantaneous velocity is negligible as the water level in the bucket drops slowly. At point B, the pressure is also atmospheric. We define the difference in elevations between the two points, zA−zB, to be Δh. With these simplifications (pA=ˉvA=pB=0) and assumptions (zA−zB=Δh), the Bernoulli equation becomes:
(33)¶Δh=ˉv2B2g
Substituting the continuity equation Q=ˉvA in the form of ˉv2B=Q2A2vc, the vena contracta coefficient in the form of Avc=ΠvcAor yields:
(34)¶Δh=Q22gΠ2vcA2or
Which, rearranged to solve for Q gives The Orifice Equation:
(35)¶Q=ΠvcAor√2gΔh
pc.RATIO_VC_ORIFICE
pc.flow_orifice(Diam, Height, RatioVCOrifice)
Returns flow through
a horizontal orifice.pc.flow_orifice_vert(Diam, Height, RatioVCOrifice)
Returns flow
through a vertical orifice. The height parameter refers to height
above the center of the orifice.There are two configurations for an orifice in the wall of a reservoir of water, horizontal and vertical, as the image above shows. The orifice equation shown in the previous section is for a horizontal orifice, but for a vertical orifice the equation requires integration to return the correct flow. You will explore this in the Flow Control and Measurement Design Challenge.
Section Summary¶
- Bernoulli vs energy equations: The Bernoulli equation assumes that energy is conserved throughout a streamline or control volume. The Energy equation assumes that there is energy loss, or head loss hL. This head loss is composed of major losses, hf, and minor losses, he.
Bernoulli equation:
Energy equation, simplified to remove pumps, turbines, and α factors:
- Major losses: Defined as the energy loss due to shear between the walls of the pipe/flow conduit and the fluid. The Darcy-Weisbach equation is used to find major losses in both laminar and turbulent flow regimes. The equation for finding the Darcy friction factor, f, changes depending on whether the flow is laminar or turbulent. The Moody diagram is a common graphical method for finding f. During laminar flow, the Hagen-Poiseuille equation, which is just a combination of Darcy-Weisbach, Reynolds number, and f=64Re, can be used
For water treatment plant design we tend to use plant flow rate, Q, as our master variable and thus we have.
f for laminar flow:
f for turbulent flow:
Hagen-Poiseuille equation for laminar flow:
- Minor losses: Defined as the energy loss due to the generation of turbulent eddies when flow expands. Once more: minor losses are caused by flow expansions. There are three forms of the minor loss equation, two of which look the same but use different coefficients (K′ vs K) and velocities (ˉvin vs ˉvout). Make sure the coefficient you select is consistent with the velocity you use.
First form:
Second form:
Third and most common form:
- Major and minor losses vary with flow: While it is generally important to know how increasing or decreasing flow will affect head loss, it is even more important for this class to understand exactly how flow will affect head loss. As the table below shows, head loss will always be proportional to flow squared during turbulent flow. During laminar flow, however, the exponent on Q will be between 1 and 2 depending on the proportion of major to minor losses.
Head loss scales with: | Major Losses | Minor Losses |
---|---|---|
Laminar | Q | Q2 |
Turbulent | Q2 | Q2 |
- The head loss trick, also called the control volume trick, can be used to incorporate the ‘kinetic energy out’ term of the energy equation, ˉv222g, into head loss as a minor loss with K=1, so the minor loss equation becomes (1+∑K)ˉv22g. This is used to be able to say that Δz=hL and makes many equation simplifications possible in the future.
- Orifice equation and vena contractas: The orifice equation is used to determine the flow out of an orifice given the elevation of water above the orifice. This equation introduces the concept of a vena contracta, which describes flow contraction due to the inability of streamlines to make sharp turns. The equation shows that the flow out of an orifice is proportional to the square root of the driving head, Q∝√Δh. Depending on the orientation of the orifice, vertical (like a hole in the side of a bucket) or horizontal (like a hole in the bottom of a bucket), a different equation in aide_design should be used.
The Orifice Equation: